致力于持续不断的产品创新、效率提升、成本降低与品质提高,从而在日渐激烈的市场竞争中脱颖而出,无疑是现代制造业的普遍追求。为此,各种现代的制造技术,如CAD(计算机辅助设计技术)、CAM(计算机辅助制造)、CIM(计算机集中管理)、高性能数控加工中心、网络系统以及先进的生产管理系统(ERP)在企业当中得到了广泛应用与推广。
今天,在现代化的工厂,不仅是设计和制造环节实现了电脑化和数字化,连同物品出入库管理、生产管理以及各工序管理,凡是与制造相关的一切过程全面依靠计算机统一管理与规划,操作现场的CAD、CAM、CAE的各个系统均经由网络统一到主计算机进行管理。通过全面依靠无缝连接从设计到生产的各个环节,这些技术实现了制造效率和产品品质较以往的提升,并不断做得更好。
以PC-DMIS为核心的EMS企业计量解决方案,在企业现有CAD系统、先进生产管理系统和网络技术的基础上,实现了将用户的计量操作从设计一直延伸到最后的检测,改传统的蓝图打印为现代的无纸数字化检测。
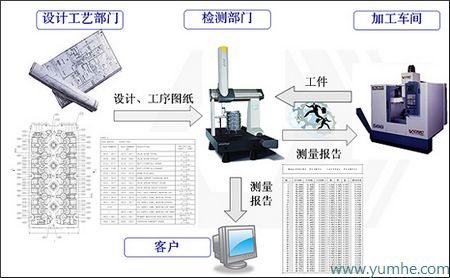
我们知道,当前很多工厂的检测过程是这样实现的:设计和工艺部门将设计和工艺规划以纸面方式传递到检测部门,检测部门需要根据图纸要求进行测量机的联机编程,这样做一方面需要检测部门花费大量的时间和精力进行图纸分析,另外一方面还要浪费测量机宝贵的机时,同时检测信息的传递缓慢,最后的检测报告不便于管理,共享和追溯困难,从而使得工厂的整个检测环节效率低、难于与现代以数字为显著特征的工厂制造进行紧密融合。
测量技术的发展为数字化检测铺平了道路
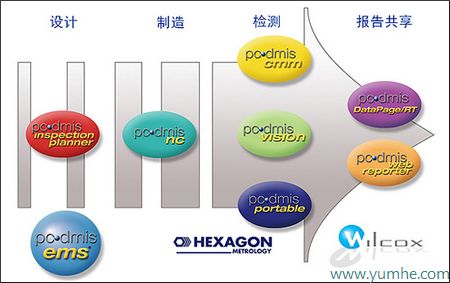
EMS企业计量解决方案,以软件为平台,不仅充实了用于计量检测环节的测量技术,同时还将测量延伸到了设计环节 – PC-DMIS检测规划(PC-DMIS Inspection Planner)、制造环节 - PC-DMIS NC以及最终的报告共享(PC-DMIS Web Reporter),提供了一整套完成的、可升级与相互兼容的软件组件,面向从小型的车间一直到跨国工厂,用来监控和管理整个系统的质量。整套系统的工作类似于Microsoft® Office,各单个产品具有相似的外观和操作感受,同时还便于进行数据共享,在一些情况下还可以相互间共享检测程序。
在CAD设计环节,PC-DMIS 检测规划自动能够读取来自CAD的检测信息,并通过脱机编程(PC-DMIS Offline)的方式进行检测程序的编制、模拟测试与路径优化。所有的通过脱机编程编制的程序通过企业中心数据库进行存储。测量机可根据生产管理系统的指令从中心数据库进行相应检测程序的调用,检测完成后,自动检测测量结果上传到中心数据库,供生产管理系统使用。所有来自检测系统的测量数据可通过统计分析软件和网络报告器进行统计分析,并可使得不同的人按照不同的权限浏览相关的产品信息。
以下是关于数字化检测过程的简单示意图:
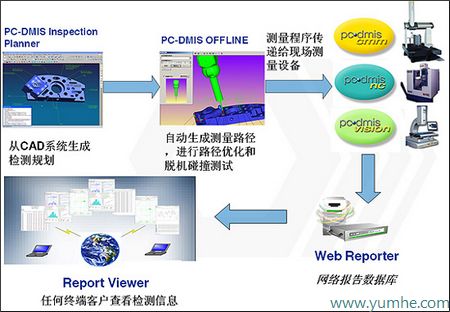
所有的测量过程都是通过先进计算机、软件和网络技术进行,能够快速适应设计的变化,并可及时实现对整个制造过程的调整。
技术要点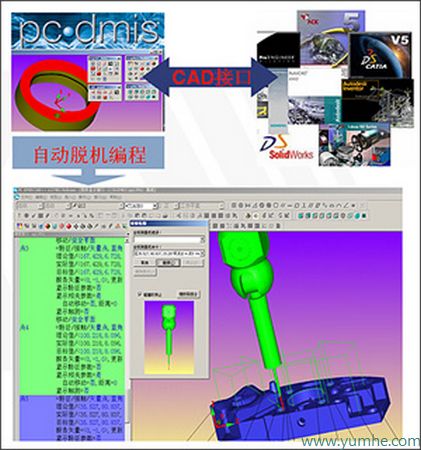
在整个数字化检测过程中,我们主要通过检测规划-脱机编程-联机检测-网络数据化管理等核心环节实现。
- PC-DMIS Planner – 将设计意图转化到检测程序中
PC-DMIS IP连接设计和检测,使得无纸化检测成为现实。CAD设计人员利用电子方式标注图纸,这些符号成为了CAD模型的一部分,通过CAD直读接口功能,直接导入多种CAD软件格式的零件GD&T国际标准的质量检测信息
导入IP文件自动生成测量程序,并自动优化测量路径,进行脱机碰撞测试,保证程序的可靠性。
各种测量设备通过PC-DMIS执行测量程序,测量结束后软件自动输出和保存检测报告。
检测报告的网络数据化管理:
各种计量设备分布在客户各生产环节,通过网络报告系统可以实时远程查看和监控所有测量单元的产品质量:
- ◆PC-DMIS Web Reporter:网络报告数据库,对客户现场的各种计量设备的测量结果进行数据整合和网络化信息管理。
- ◆PC-DMIS Report Viewer:任何客户端可以通过安装报告浏览器实时快速查看零件检测数据
- ◆PC-DMIS Report Designer:专门提供客户定制个性化报告模板,更加灵活方便
总结
通过数字化检测体系的构建,实现了效率提高、成本降低和品质提升:
- 建立了跨部门/跨工厂的检测数据管理体系
- 构架了基于信息系统的高效反应和决策体系
- 减少了测量过程的人为错误和意外损失
- 增强了数据的方便性,安全性,真实性和一致性
- 强化了检测数据的可利用性和历史追溯性
|